Cooling tower is considered as a necessary cooling and cooling device in the process of using industrial equipment. But some tower problems are misleading, leading to incorrect tower selection. Affects the system that needs cooling and cooling. The following article of the company P69 will help you read about the most accurate cooling tower.
What is a cooling tower?
What is English cooling tower? A cooling tower is a device used to reduce the temperature of the water in the HVAC system by capturing the heat of that water and then releasing the heat to the atmosphere. The water-heating mechanism is intended to cool down machinery, equipment, the environment inside the factory, and the air-conditioning system.
Cooling towers are applied in industries such as refrigeration, plastic industry, seafood, metallurgy, pharmaceuticals or electric cables. It is a device used to reduce the temperature of a water stream by extracting heat from the water and releasing it to the atmosphere. Cooling towers take advantage of evaporation so that water is evaporated into the air and released into the atmosphere. As a result, the remaining water is considerably cooled. Cooling towers can also lower water temperatures than devices that only use air to remove heat such as car radiators, and so using a cooling tower is more energy efficient. quantity and cost.
Structure of the cooling tower
A basic cooling tower is composed of the following components:
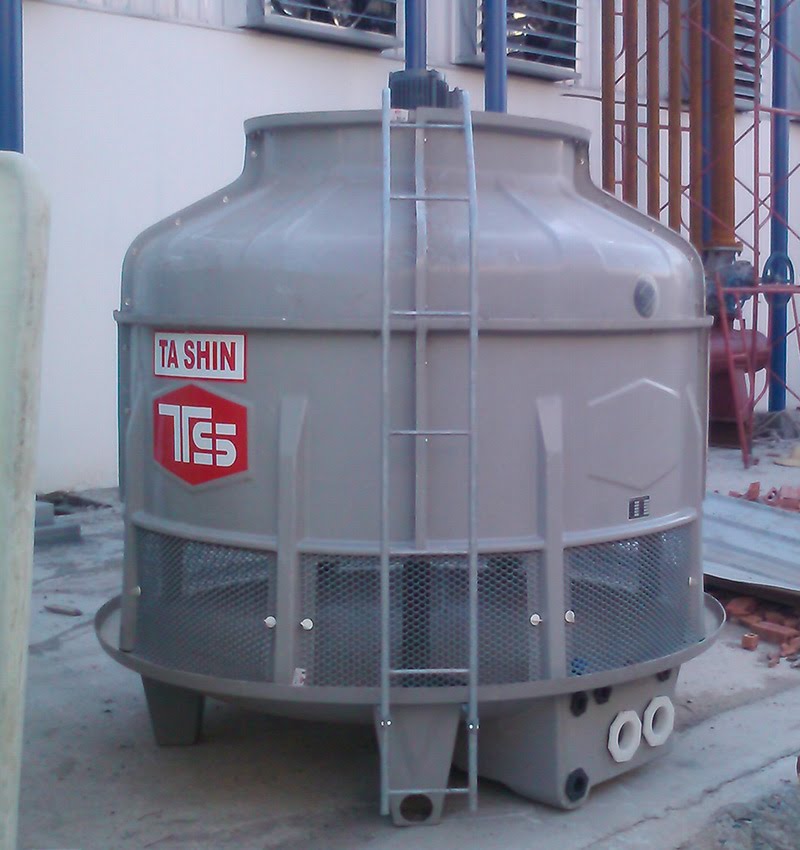
1. Tower body and tower frame
The frames of large cooling towers will be made of metals or alloys. The outside will be surrounded by the tower shell. In some smaller models, the body and frame are combined into one. Usually made from fiberglass or stainless steel with the advantages of not being mossy, anti-aging and corrosion, easy to clean and have a fairly long life.
2. Blower
This part is responsible for blowing the air circulating in the tower from the bottom to the top. Let the air do the water cooling function. The large capacity towers with fans are made from extremely durable aluminum alloy. For smaller models, the propeller will be made of high-strength ABS plastic.
3. Nozzle
Has the effect of spraying and distributing the water evenly on the surface of the heatsink. Helps increase the cooling efficiency of the tower. The nozzle manufacturing material is also based on the same capacity as the blower. Large capacity cooling towers will have nozzles made from aluminum alloy while smaller models are made from ABS plastic.
4. Radiator plate
Crafted from wood or plastic. This part is responsible for evenly distributing the water, thereby helping the air pass through to get more heat from the evaporation process. Increases the water cooling efficiency of the tower. There are two main types of heat sinks: film and spray. Membrane form is designed from thin plastic films that are joined together. Water falling from above will form a thin film of water. Increase the area of water that is exposed to the air. The spray form will cause the water to splash into smaller particles. This also increases the contact area of the water that needs to be cooled with the air.
5. Water tank
The water tank will be installed at the bottom of the tower. Used to store water after it has been cooled. Water tanks are usually designed with a low point or have a water collector. Return the cooled water to the duct to return to the water-requiring cooling cycle.
Above are some basic parts of the cooling tower, in addition, the cooling tower also has some parts such as gearbox, reducer, water shield, …
Working principle of cooling tower
There are different types of cooling towers on the market. However, they are still based on a fairly similar operating principle and most operate on the principle of “evaporative cooling”. Currently, there are two types of cooling towers:
1. Round cooling tower
When starting the cooling tower , water will be sprayed from the top to the radiator plate in the form of a jet through the sprinkler system and the water divider of the device.
Meanwhile, the cooling tower principle will use cool air from the outside to enter the tower at the inlet located at the bottom of the tower. The air will move back up, pass through the radiator plate, contact the water and carry the hot steam to the outside environment.
The remaining cool water in the tower, reduced from 5 – 12°C (depending on the tower line) compared to the original temperature, will be taken to factories, factories or large buildings to cool down machinery and office areas. After that, the hot water from the factories is brought to the cooling tower again and the cooling process is repeated as above.
2. Square cooling tower
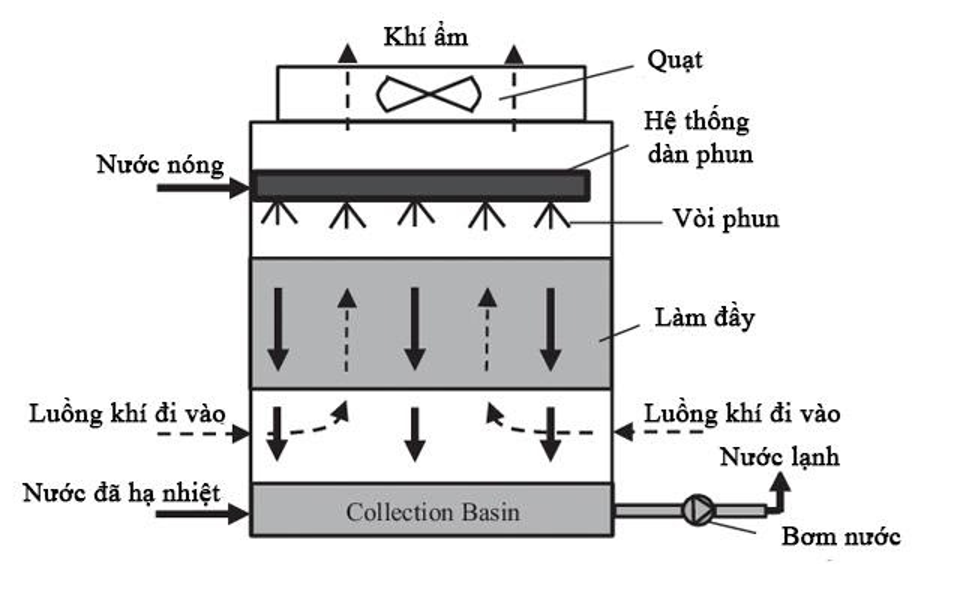
This line of cooling towers has a vertical airflow design that flows down to the water tank, in the same direction as the water flow straight down by the action of gravity. At that time, the water will be evenly distributed on the surface of the cooling film through the water distribution system in the form of a trough or nozzle.
At the same time, the circulating air will carry the hot steam to the outside environment, helping to reduce the temperature of the water in the circulating system. Finally, similar to the circular water cooling tower, cool water will be brought to the factory to cool the machinery and equipment here.
Common situations encountered in cooling towers
The problems that most cooling towers often face during operation are scale, corrosion and microbial growth. The water used always contains impurities that cause scale and corrosion in the cooling tower. Inside the cooling tower there is always a combination of hot water and air. This inadvertently creates a suitable environment for microorganisms to grow inside the tower.
Solids and dust can be inadvertently introduced into the air by the blower blowing into the tower causing scale formation or following the water flow to other industrial equipment and damaging them. In the long run they can cause pipeline blockages.
The next problem is corrosion due to water containing impurities. They then react with metal parts in the cooling tower. As a result, the metal loses its inherent properties, the pipeline is corroded leading to leaks or worse, pipe breakage.
What are cooling towers used for?
Nowadays, the cooling tower system is commonly used in life and production by the following main functions:
1. Increase work efficiency
A production line in a factory is a combination of many types of equipment and machines working together. This will produce a large heat source and cause the engine to heat up quickly, and more machine parts will wear out.
This has a serious impact on the machine’s performance. Therefore, businesses are forced to use cooling towers to reduce the temperature in the workshop, help machines operate continuously, durable and bring more optimal performance.
However, to achieve optimal cooling efficiency, users must calculate to choose the type of cooling tower that best suits the cooling needs of the business. Because if you choose a type with a small capacity, it will not meet the cooling needs, and if you choose a tower with too large capacity, it will cause waste.
2. Reduced operating costs
The use of a cooling tower not only helps to improve working efficiency, but it also helps businesses save costs such as:
- Machine repair costs: When the machinery is operated smoothly and stably, it will minimize the breakdown and damage. This also means that businesses will not spend too much money to repair and maintain machines regularly,
- Saving electricity and water costs: With a closed operation process, the water source will be reused. Moreover, the use of this water cooler also saves significant power consumption. Because businesses will not need to install and operate large air conditioning systems. Thereby, helping businesses save on electricity and water bills.
3. Environmental protection
Industrial water cooling towers work by evaporating water into the atmosphere to remove heat from the water. Therefore, it does not consume too much electricity and limits the loss of machinery lubrication. This contributes to preserving the living environment and avoiding negative impacts on the environment.
When to use a cooling tower system?
Cooling towers are used to cool systems with water and wind cooling capabilities. Users should invest and install a cooling system in the following cases:
- The heat output of the system is large, requiring cooling for the machinery to ensure the safety of the equipment and the operator.
- Units with machinery and equipment operating continuously, need to use cooling towers to ensure working performance.
- It is necessary to use a cooling tower to meet the needs of using air conditioning, or used in frozen products such as seafood, meat, livestock, poultry, agricultural products,….
- Need to be used to cool machines that produce aluminum billets, steel, plastic injections, electrical cables, pharmaceuticals,…
Contact us today for a free consultation and answer at:
Contact information P69 – M&E Contractor
Address: No. 6/165C Xuan Thuy, Cau Giay District, Hanoi
Website: https://p69.com.vn/
Hotline: 02422121212 – 0965937799
Email: kd@cokhip69.com.vn
Facebook: https://www.facebook.com/p69nhathaucodien
LinkedIn: https://www.linkedin.com/in/congtyp69/
Youtube : https://www.youtube.com/channel/UCOUwCnE5iGj8iqe_ZIUM7oA